What is Electrically Conductive Adhesive?
Electrically Conductive Adhesive is used for high-reliability applications such as electronics, automotive, medical, and consumer products, where components need to be held in place and electrical current can be passed between them.
To sum up, it means adhesive should meet two main requirements: bonding ability and electrically conductive ability to become an effective electrically conductive adhesive.
Type of Electrically Conductive Adhesive
Electrically Conductive Adhesive can be based on several different chemistries:
Electrically conductive silicone adhesive
These can be graphite-filled and are often used for EMI/RFI shielding or for antistatic systems.
Features:
- Very high viscosity, thick consistency making them suited to larger applications such as gaskets or bonding / sealing large areas.
- The electrical conductivity is limited (so they are not a good replacement for solder).
- Volume resistivity is typically about 0.09 Ohms∙cm.
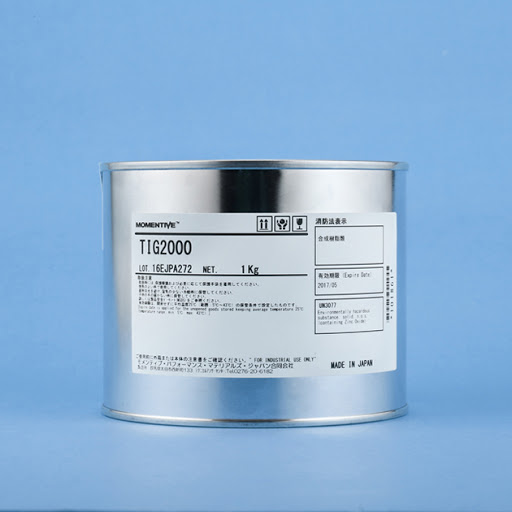
Two-component epoxy adhesive
These comprise resin and hardener
Features:
- Available in a range of viscosities (if heavily filled with a conductive metal, viscosity can become quite high).
- If filled with silver, volume resistivity can be as low as 0.0001 Ohms∙cm.
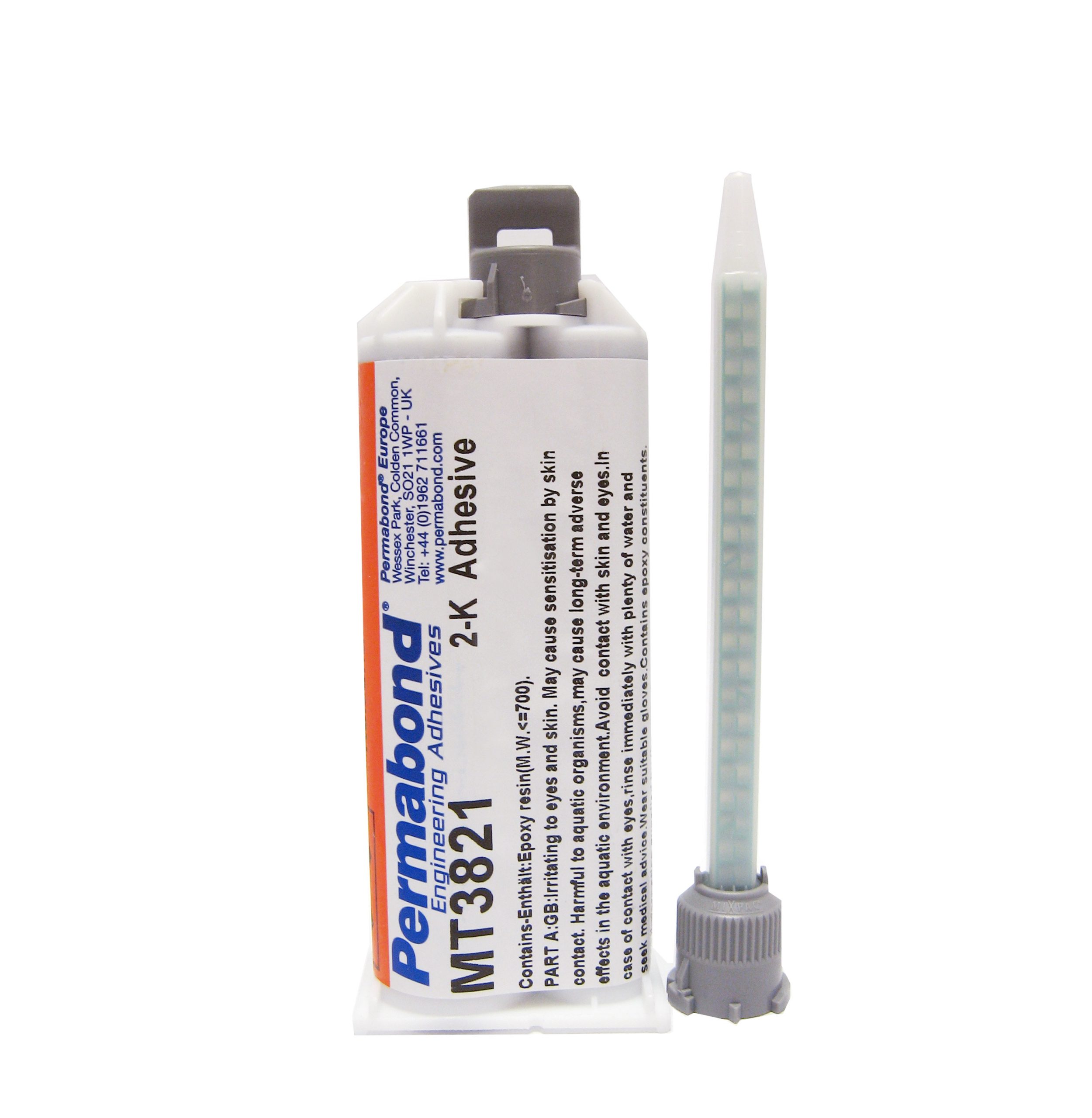
One component epoxy adhesive
These are normally heat cured so care must be taken to choose a cure schedule that won’t compromise sensitive electronic components.
Features:
- Snap-cure frozen epoxies are also popular in the electronics industry.
- Require freezer storage and cure once they reach room temperature. These can be expensive to transport and store.
- A silver-filled one-part epoxy can achieve conductivity as high as a similarly filled two-part epoxy.
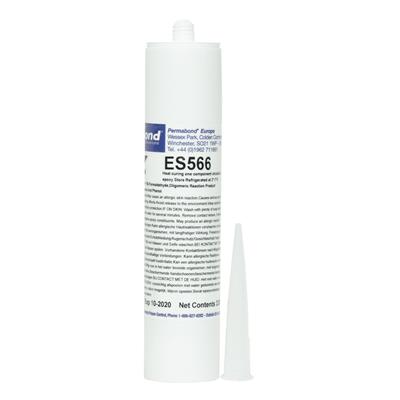
Silver-filled polyurethane adhesives
These are starting to appear on the market.
Features:
- They are two-part adhesives, so they either require mixing or they are supplied pre-mixed and frozen like the snap-cure epoxies.
- They offer high peel strength and flexibility.
- As they are silver-filled, high levels of conductivity can be achieved (around 0.0001 Ohms∙cm to 0.0004 Ohms∙cm).
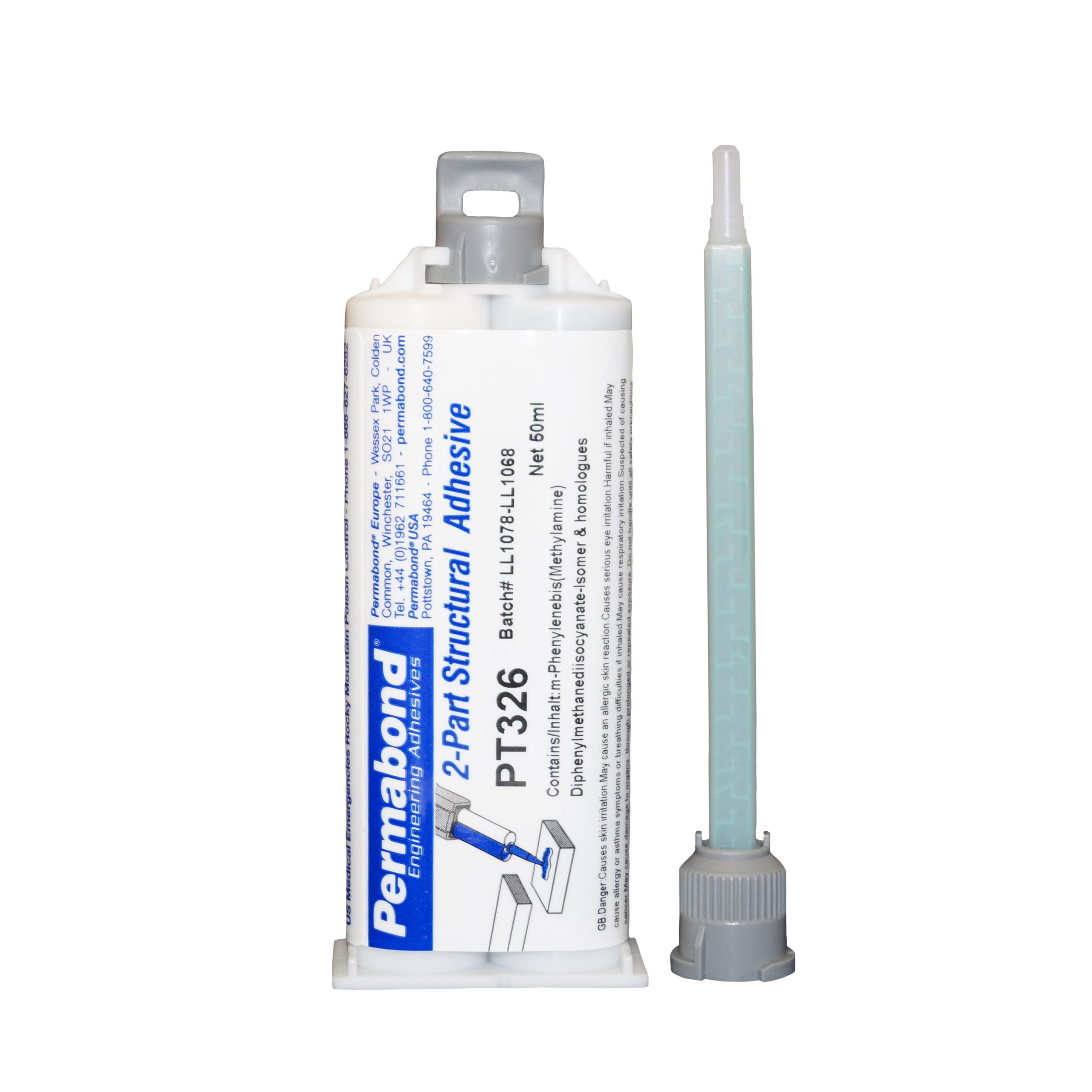
How to select a right Electrically Conductive Adhesive
There are some vital points to consider when selecting an electrically conductive adhesive:
- Level of electrical conductivity (or volume resistivity).
- Viscosity and rheology of the adhesive – does it need to flow well or stand as a proud drop (with high “wet” strength).
- Filler particle size – what is acceptable or necessary?
- Curing mechanism and cure speed – how do you plan to cure the adhesive e.g., two component mix and then room temperature cure, or heat cure – if the application involves temperature sensitive components, is a heat cure suitable? How quickly does the adhesive need to cure?
- Production line considerations – how fast is the throughput? Is the process fully automated or manual? How will the adhesive be dispensed?
- Nature of the materials being bonded, and level of adhesion required – joint design, strength required, any differential thermal expansion and contraction, Thermal conductivity, glass transition temperature, flexibility requirements.
- Environmental service conditions – temperature, exposure to chemicals, humidity, etc.
- Tests that the adhesive must pass e.g., drop tests, accelerated aging tests.
- Colour, smell, health and safety considerations, shipping, storage, and shelf life.
- And not forgetting one of the most important considerations – cost!
Typical Applications of Electrically Conductive Adhesive
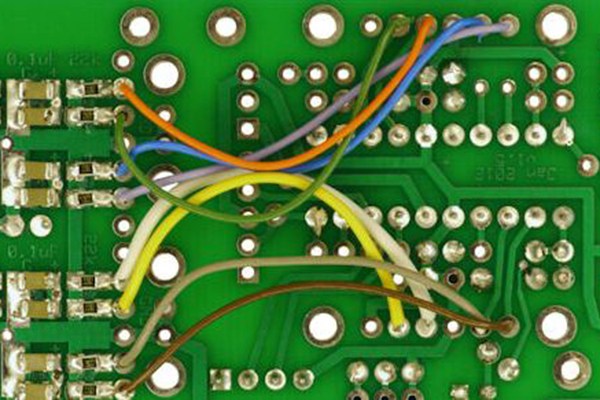
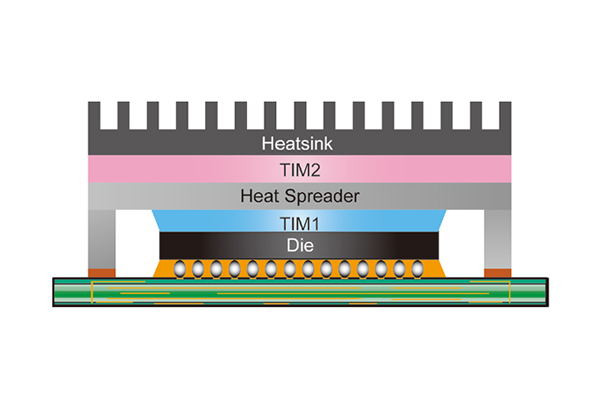
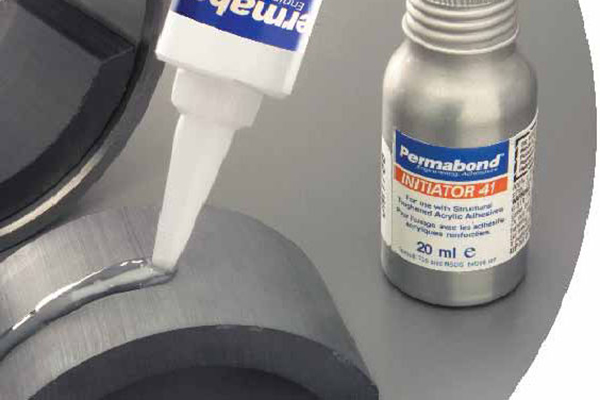
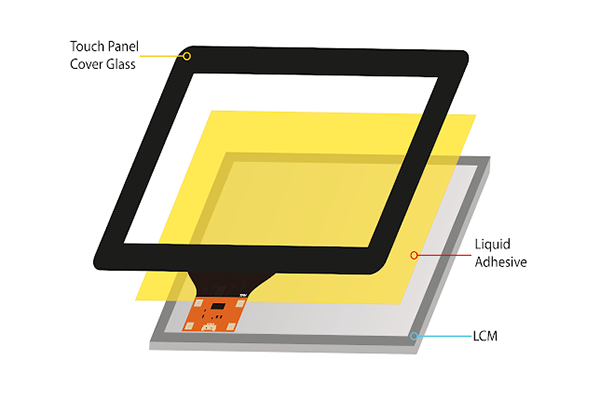
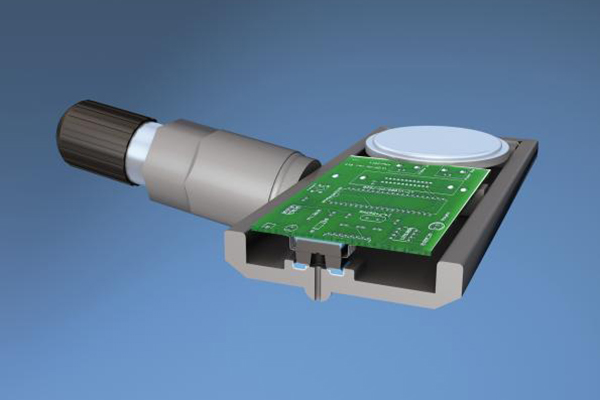
- Wire tacking
- Bonding heat sinks
- Bonding of surface mount devices to PCBs
- Potting and encapsulation of electronic components
- Component rigidising
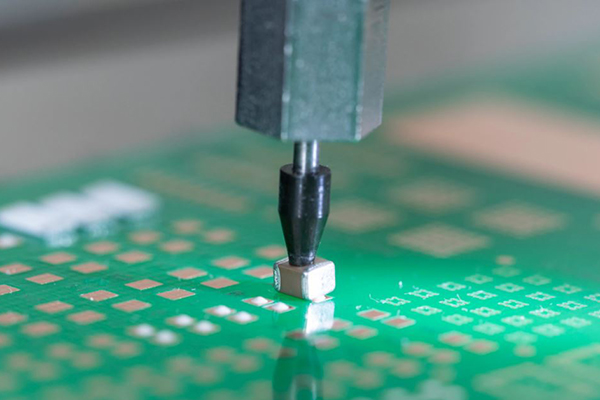
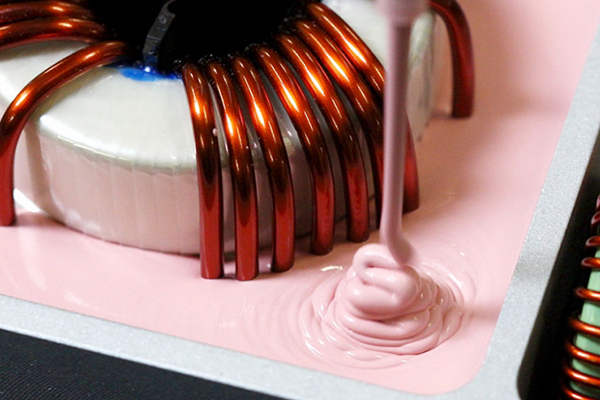
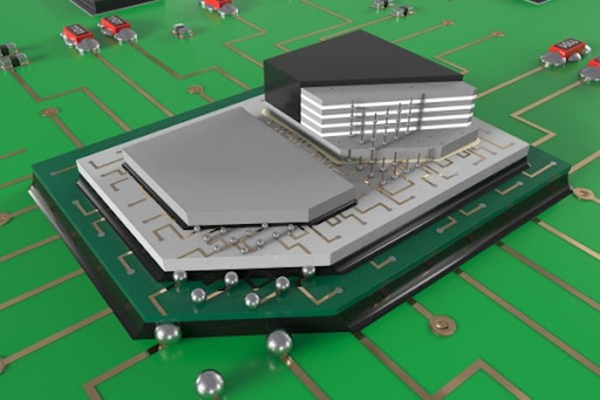
- Conformal coating to protect electronic components / PCBs
- Applications within batteries and battery packs
- Strain protection for leads/plugs
- Torroid bonding
- Coil winding
- Magnet bonding & electric motor applications
- Bonding electronics housings and enclosures
- Bonding touch screens and keypads
- Sensor bonding / potting
- Electrical transformers
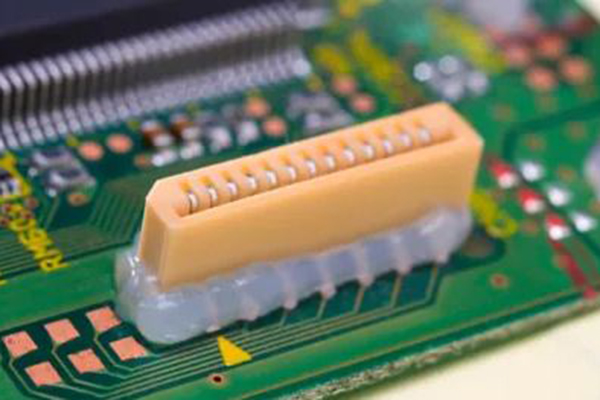